How NovoTrack's Prefabricated Rubber Running Tracks are Made
NovoTrack has established itself as a leading brand in the realm of athletic track surfaces, specializing in high-quality prefabricated rubber running tracks. These tracks are renowned for their durability, performance, and safety. Understanding how NovoTrack's prefabricated rubber running tracks are made offers insight into the meticulous processes and advanced technologies that set them apart in the industry. This article will take you through the step-by-step process of creating NovoTrack's premier athletic track surfaces.
Material Selection
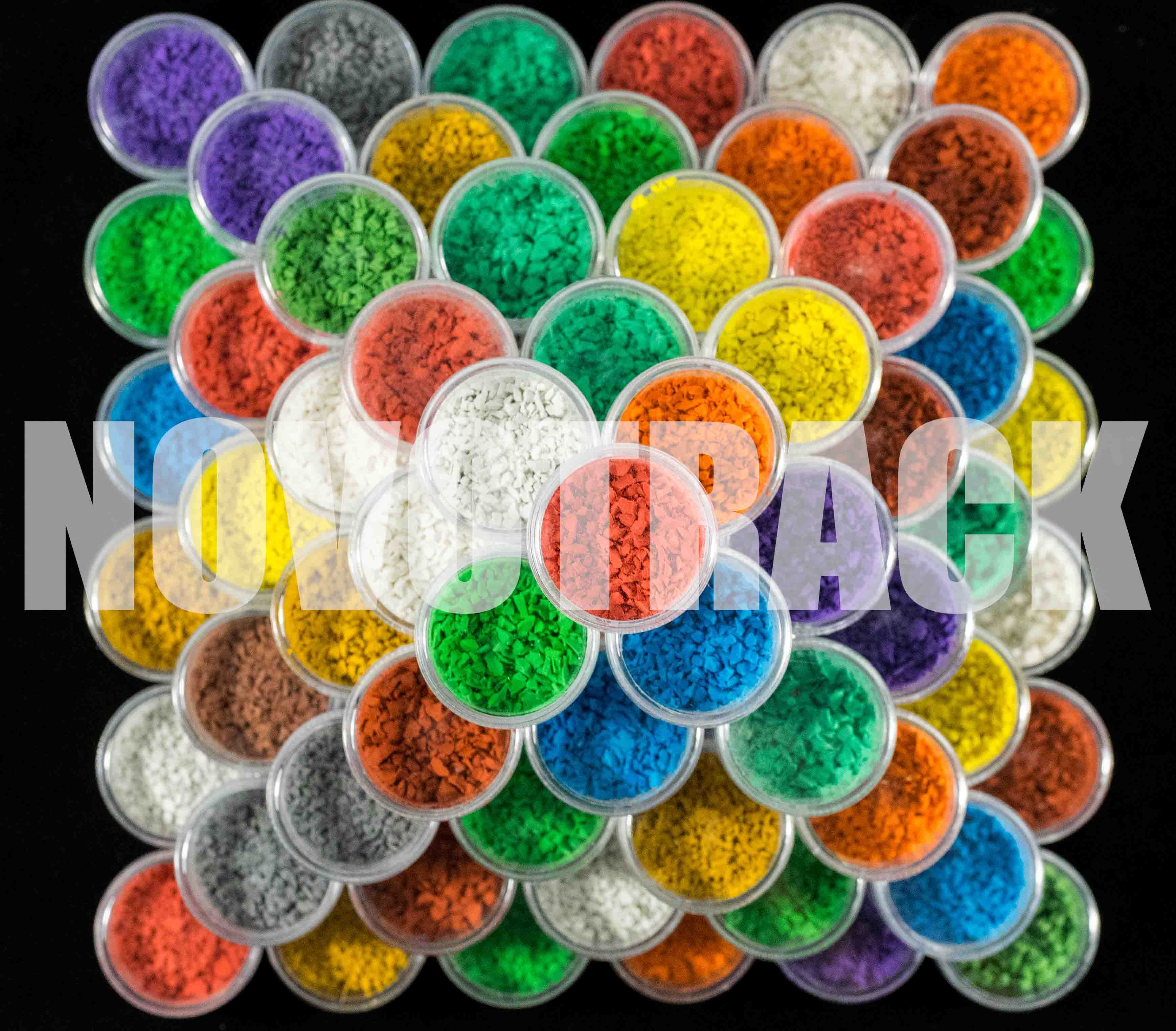
The creation of a high-quality prefabricated rubber running track begins with the careful selection of raw materials. NovoTrack sources premium recycled rubber and advanced polymers to ensure the final product is both durable and environmentally friendly. These materials are chosen for their elasticity, resilience, and ability to withstand heavy use and varying weather conditions.
1. Recycled Rubber: The primary component, providing flexibility and shock absorption.
2. Binding Agents: High-performance polymers that bind the rubber granules together, enhancing strength and durability.
Mixing and Compounding
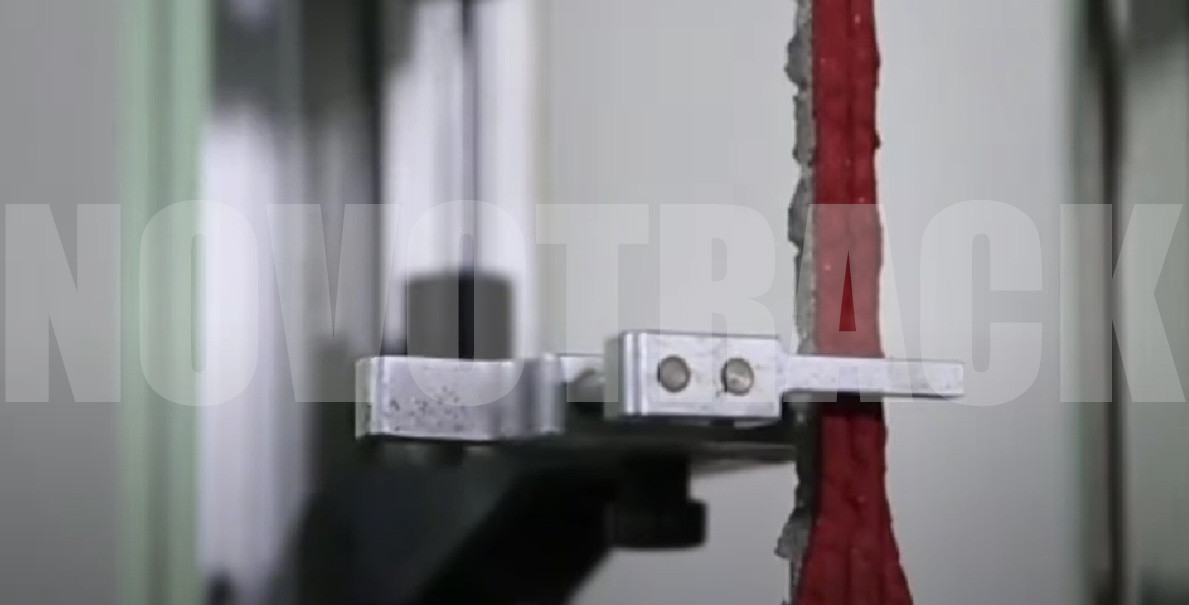
Once the materials are selected, they are sent to the mixing and compounding stage. Here, the recycled rubber granules and binding agents are combined in precise proportions to create a homogeneous mixture. This process ensures that the rubber running track material is consistent in quality and performance.
1. Homogenization: Ensures uniform distribution of rubber granules and binding agents.
2. Quality Control: Continuous testing during this stage to ensure the mixture meets NovoTrack’s stringent standards.
Vulcanization
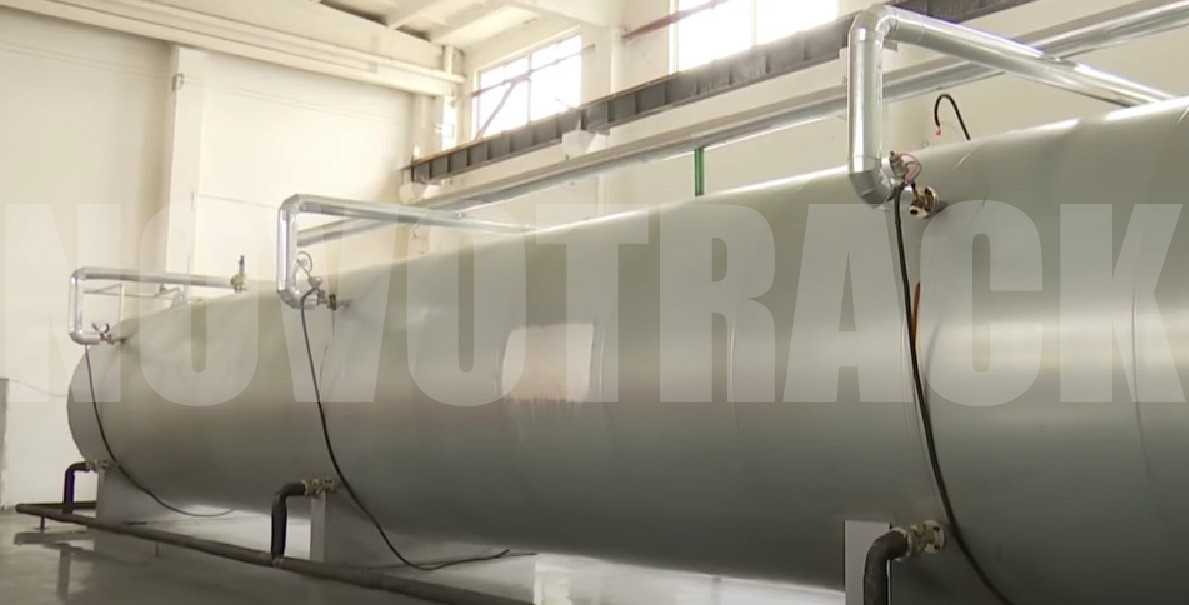
Vulcanization is a critical step in the manufacturing process, where the rubber mixture is heated and cured. This process enhances the rubber’s elasticity, strength, and durability, making it suitable for high-performance athletic track surfaces.
1. Heating: The mixture is subjected to controlled heat to activate the vulcanization process.
2. Curing: The rubber is cured to achieve the desired properties, such as improved resilience and resistance to wear and tear.
Prefabrication
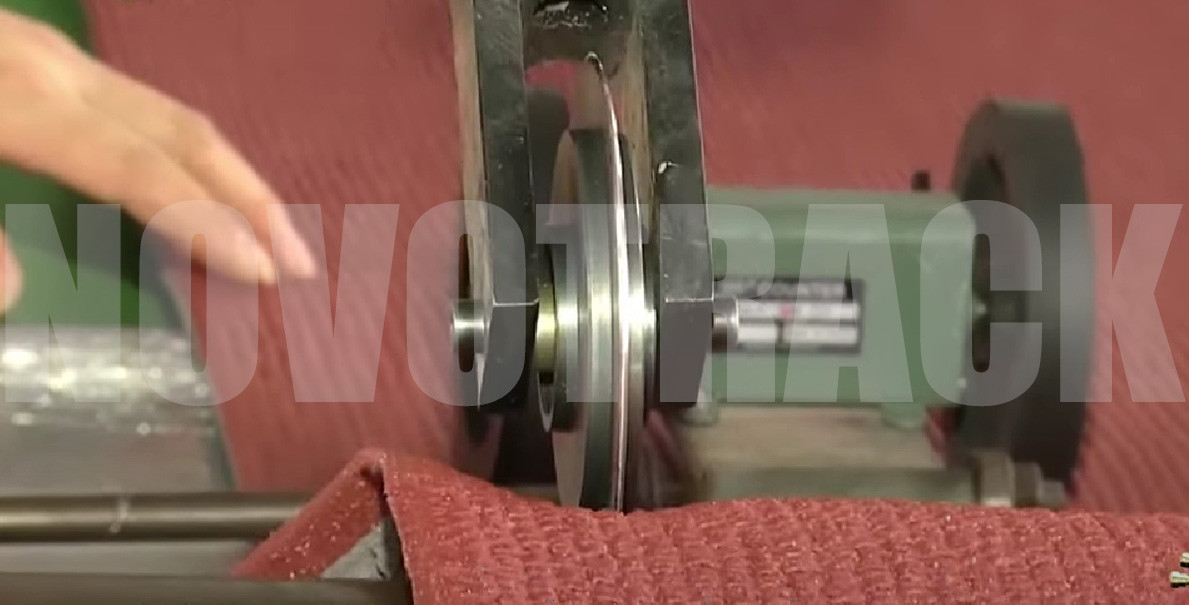
In the prefabrication stage, the vulcanized rubber is shaped into large sheets or sections that will form the final track surface. These sections are manufactured in a controlled environment to ensure precision and consistency.
1. Molding: The rubber mixture is poured into molds to create sheets of uniform thickness and texture.
2. Cutting: The molded sheets are cut into sections that are easy to transport and install.
Surface Treatment
To enhance the performance and longevity of the athletic track surface, a special surface treatment is applied. This treatment improves the track’s grip, reduces wear, and provides UV protection.
1. Sealing: A polyurethane coating is applied to seal the surface and protect against environmental factors.
2. Texturing: The surface is textured to provide optimal traction for athletes, reducing the risk of slips and falls.
Quality Assurance
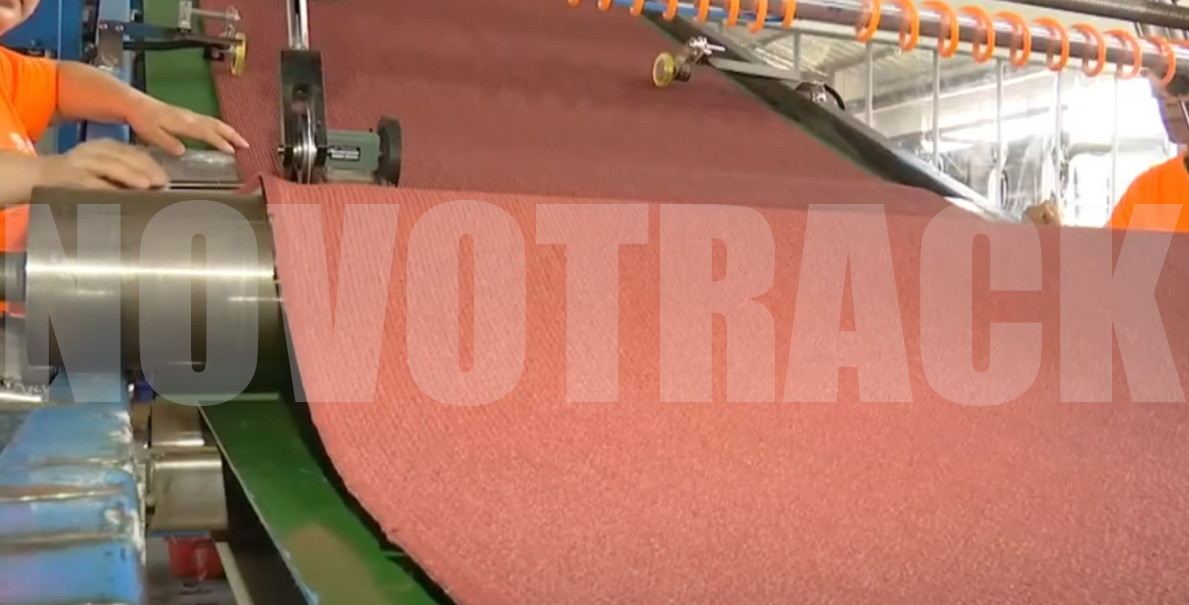
Quality assurance is a cornerstone of NovoTrack’s manufacturing process. Each section of the prefabricated rubber running track undergoes rigorous testing to ensure it meets the highest standards of performance and safety.
1. Durability Testing: Simulating heavy use to ensure the track can withstand intense athletic activity.
2. Performance Testing: Evaluating the track’s shock absorption, traction, and overall performance under various conditions.
Quality Assurance

Quality assurance is a cornerstone of NovoTrack’s manufacturing process. Each section of the prefabricated rubber running track undergoes rigorous testing to ensure it meets the highest standards of performance and safety.
1. Durability Testing: Simulating heavy use to ensure the track can withstand intense athletic activity.
2. Performance Testing: Evaluating the track’s shock absorption, traction, and overall performance under various conditions.
Installation
The final step is the installation of the prefabricated rubber running track. NovoTrack’s installation team ensures that the track is laid down with precision, providing a seamless and high-performance athletic track surface.
1. Site Preparation: The existing surface is cleaned and leveled to provide a stable foundation for the new track.
2. Track Laying: Prefabricated sections are carefully positioned and bonded, creating a continuous and durable running surface.
Conclusion
The meticulous process behind the creation of NovoTrack’s prefabricated rubber running tracks ensures that each track meets the highest standards of quality, performance, and safety. From the careful selection of materials to the precise installation, every step is designed to produce a superior athletic track surface. NovoTrack’s commitment to excellence and innovation has made their rubber running track material the preferred choice for sports facilities worldwide.